Working on pottery is not everyone’s cup of tea. It requires a lot of effort to master the skill of working with clay and giving it the shape of a pot. From throwing clay onto the wheel to firing it in the kiln, the entire process requires the utmost level of concentration and proper techniques, which take enough time to acquire by beginners. But do not worry. We know how strenuous it is to work with potteries, and that is why we are here to help you make your job easy through our tips and tricks.
Now, let’s move on to pottery firing. Whether it is bisque firing or glaze firing, pottery is just incomplete without firing it correctly. It is one of the most intricate processes that need much care and attention. Making a mistake here can ruin your whole effort and time. So be careful while firing your pottery inside a kiln or oven. Especially, beginners need to learn the techniques of firing correctly before proceeding onto furthermore bigger pottery projects. In this article, we will uphold those firing mistakes that you need to avoid while putting your piece inside a kiln or an oven. But before that, let’s know why firing is so vital in creating pots.
Why do you need to fire your pottery?
Following are given the factors of why firing your pottery is essential, so let’s have a glance.
- After firing, the clay becomes hard and sturdy. You need to fire your clay after you are done with shaping it in the form of a pot, as firing ensures the prevention of the melting away of clay when it comes in contact with moisture. In other words, the clay turns waterproof upon firing.
- Through firing, the extra moisture present in the clay dries out, and the water gets evaporated, so the clay becomes hard and durable.
- The firing gives a nice texture to your pottery so that it doesn’t feel rough or moist.
- The process of firing after glazing is done to flux and fuse the chemicals present in the glazes, thus making the pottery food safe.
- The firing after glazing makes sure that the glaze adheres to the pot surface properly.
- Last but not least, firing turns your mud pottery into a ceramic one.
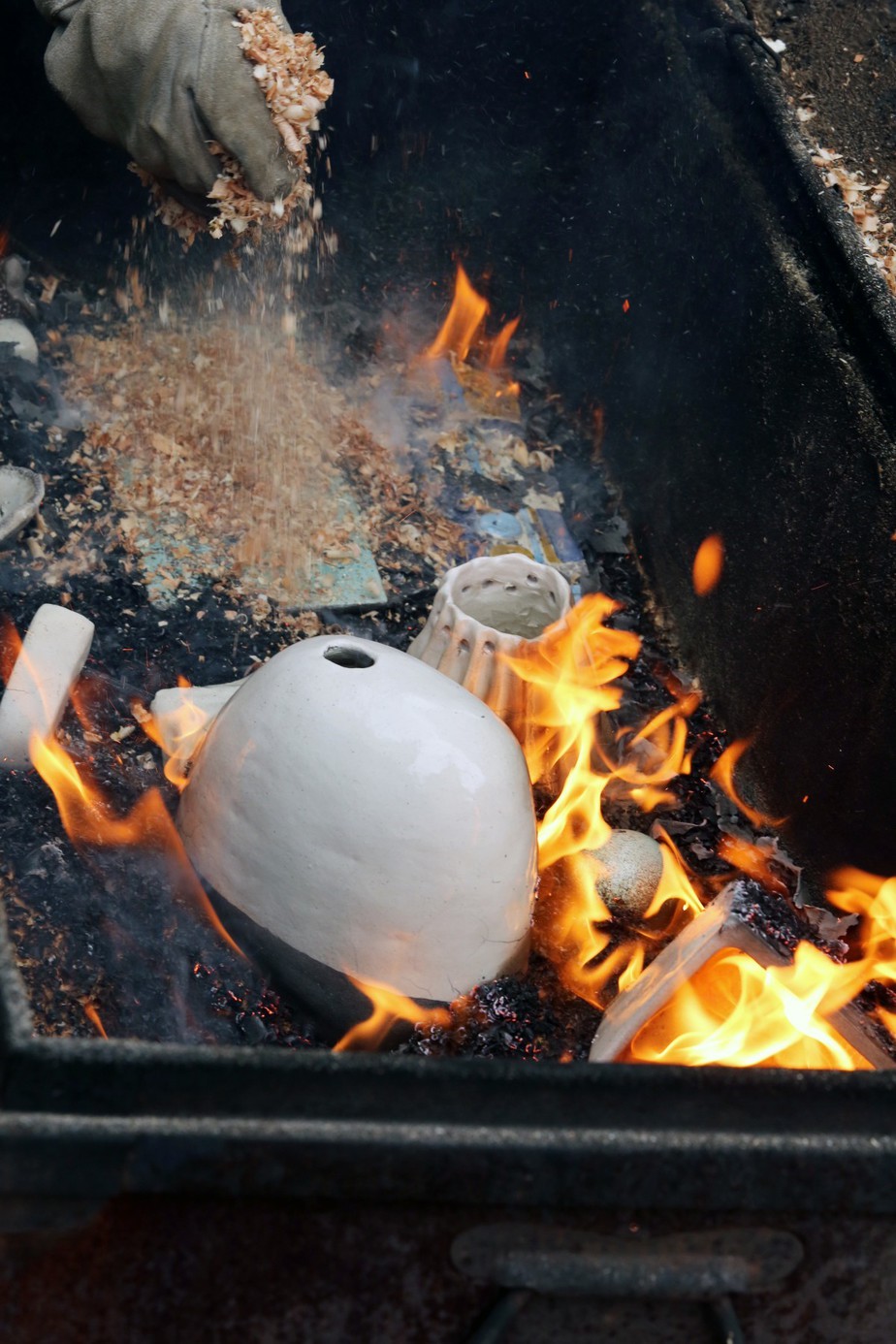
Now, you may doubt why you need to be more careful while firing. It is so because the wrong way of firing may cause cracking, breaking, and even the explosion of your pottery, which is not only disappointing but also risky. So, it is crucial to know the things that you should keep in mind while putting your pottery into the fire to avoid any such kind of failures. Here, we are going to discuss the 10 common firing mistakes that you should avoid while working on a pottery project. So without wasting more time, let’s proceed further.
1. Not understanding the clay body type:
While firing your clay, you need to know about the compatibility between the clay body type and the firing temperature range. If the temperature range doesn’t match the clay type, it might cause shrinking, sagging, warping, or cracking of the pottery piece. You must have proper knowledge about the clay body type and the cone temperature suitable for it.
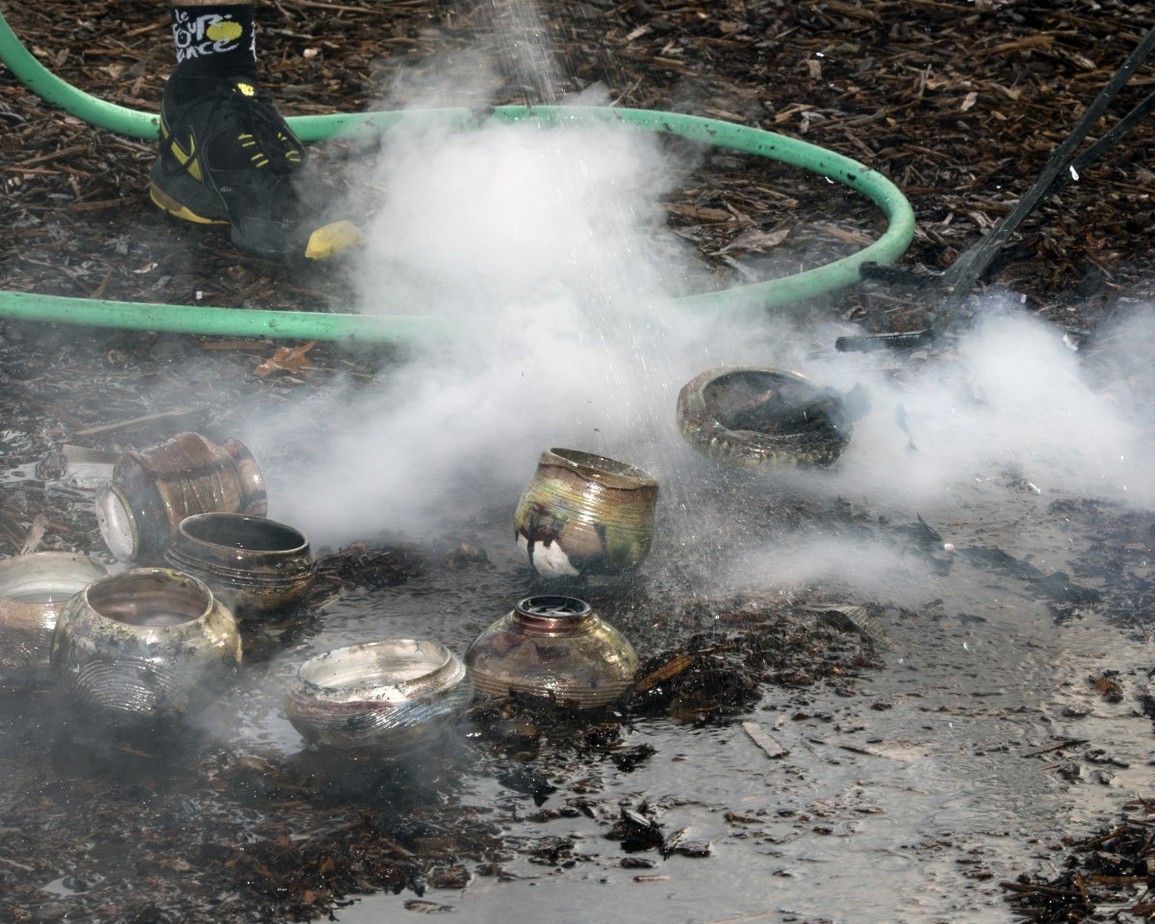
For earthenware-type clay, it is better to set it at a low-firing session as they are highly plastic and contains various mineral compounds that help it reach the optimum temperature quite quickly. While working with stoneware, it is always better to use it in the mid-range or high-range firing session to reach maturity. Also, a high firing range applies to porcelain potteries. So, it is always important to consider the suitable firing temperature range for your clay body type, as you don’t want to compromise your pottery creation.
2. Setting the wrong temperature:
The process of firing transfers heat into clay to make it stronger, more durable, and more like a stone to strengthen the material. A lot of modifications take place when a clay pot comes in contact with a direct change of heat. And finally, mud gets turned into ceramic work. So it is crucial to focus on the temperature that you will set to fire your clay. Too much firing or little firing while bisque firing may lead to the breaking or cracking of the clay, slowing down the entire process, instead, leaving the process incomplete. When it comes to firing after glazing, too high a temperature will melt the glazing compound, and too low a temperature may affect the durability of the pot. So, firing your pottery at the optimum temperature of the cones is essential.
Thus, it is necessary to know about the right temperature that your clay requires based on how much moisture it contains. Whether you need bisque fire, low fire, or high fire, you need to set your pyrometric cones at that temperature first.
Here is a chart portraying your firing temperature and cone range for a suitable type of clay body.
Kiln | Clay | Temp. | Cone Range | Kiln Color | |
Bisque | After Glazing | ||||
Low-fire | earthenware | 1745F-2012F | 015-1 | 04-06 | Yellow/ Orange |
Mid-range | Stoneware | 2124F-2264F | 2-7 | 4-8 | Orangish Yellow |
High-fire Stoneware | Stoneware | 2305F-2336F | 8-12 | 8-10 | Yellow |
High-fire Porcelain | Porcelain | 2318F-2455F | 10-13 | 10-12 | White |
3. Not drying the clay before firing:
Your kiln doesn’t like moisture. You need to keep that in mind before putting wet clay into the fire. It will cause an explosion or bursting of the pot, which is not only going to break your pottery into pieces but also make you face crucial accidents. So, never put a wet or moist pot inside a kiln or oven.
After shaping the clay into a pot, allow it to become air dry. Make it leather dry in the air, i.e., almost too dry to melt down. At this point, your greenware must be a little bit damp but not too wet which makes it workable enough. Thus, your pottery is ready for bisque firing. You can either make your pot completely dry by putting it at the low-fire range for some time or directly pass it for bisque-firing to convert it into ceramic ware.
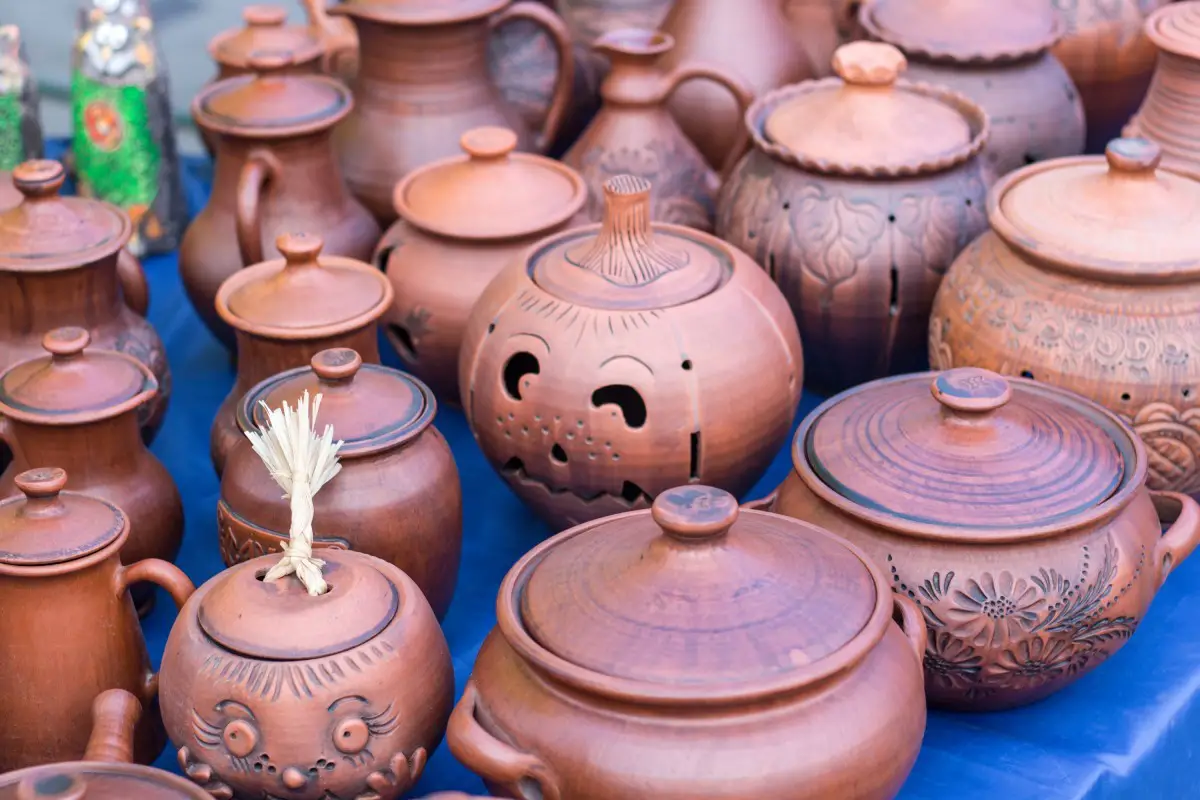
When it comes to firing after glazing, wait for some more time to make your pottery dry after applying the glazing mixture. Check by touching it if it’s completely dry or not. If the surface feels a bit cold to your touch, then you need to allow it to sit for some more time to become completely dry. Once it’s fully dry, you can transfer the piece into a kiln or oven for firing.
4. Choosing the wrong size of the kiln while firing:
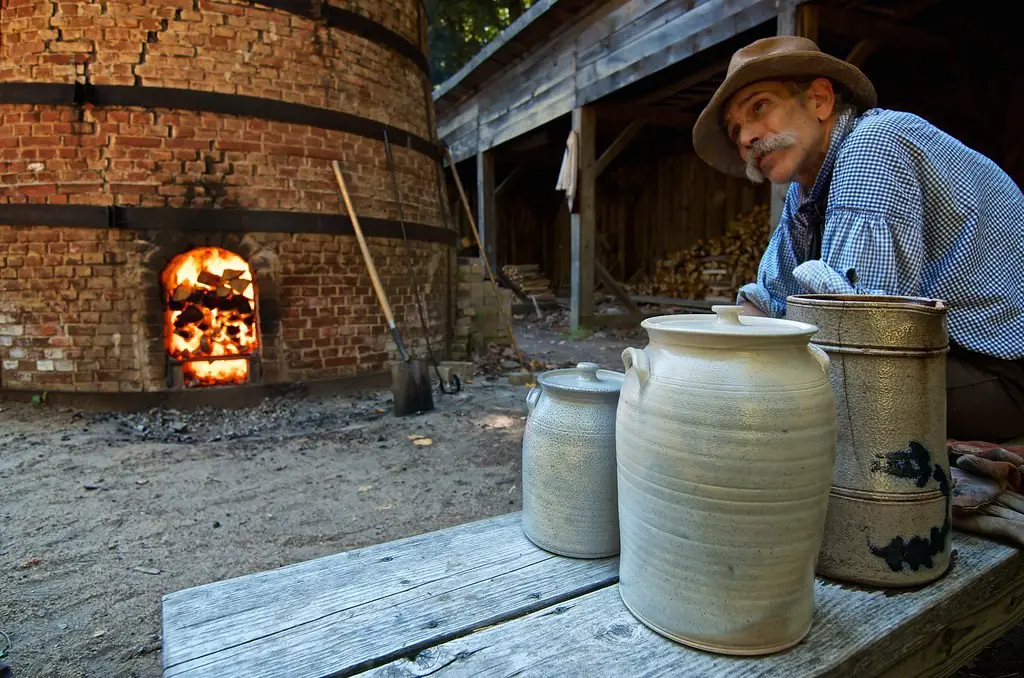
There are different sizes of kilns available in the market. There are multiple kiln sizes, starting from the size of a stove to the dimensions similar to a room. Not only does the size matter but also the type of kiln is important. Some kilns come in the form of shelves, where you need to stack the pots for firing. Undoubtedly, kilns are the best forms of tools to fire potteries than any other oven. But in this way, lining up clay pots on the shelves sometimes leads to adhering glazes from one pottery piece to another. In this way, either the pots break or the glazes ruin themselves.
So, it is always better to maintain some distance between the pottery pieces to prevent them from adhering to one another. Stacking should be done carefully, and then proceeding to fire one after another. Tumble stacking for large unglazed pottery pieces should be done by the potters who have acquired enough skill in stacking pots while firing, or else it will lead to disappointment. Also, choose the size of your kiln based on the requirement. Using a large kiln for one or two potteries is not a suitable choice, and even struggling with a small kiln while you need much space is another sign of foolishness. So, pick the right size to avoid any such kind of kiln and firing-related disappointments.
5. Not understanding the required time:
There is no space for denying the fact that pottery work is a time-taking procedure, where you can’t compromise with time. No matter how many new technologies and inventions are there to speed up the process, you can’t skip the required time if you want better and excellent results. So while putting your potteries inside the kiln for firing, if you don’t give them enough time, they will remain incomplete, which might result in cracking or breaking of the pots by hampering their durability and appearance. Thus, when you put your pottery on firing, take enough time, and keep patience until it gets completed.
Also, you should know how much time is required for the particular greenware or glaze that you are using for your pot. Not every pottery takes the same amount of time to get done with firing. The materials, properties, and moisture of the clay or glaze influence the time of firing. So first, get a piece of knowledge about it and then move on further for firing. If you want proper results, firing for a too-long or too short duration is not acceptable. So, consider the matter of timing before putting your pot inside the kiln for firing.
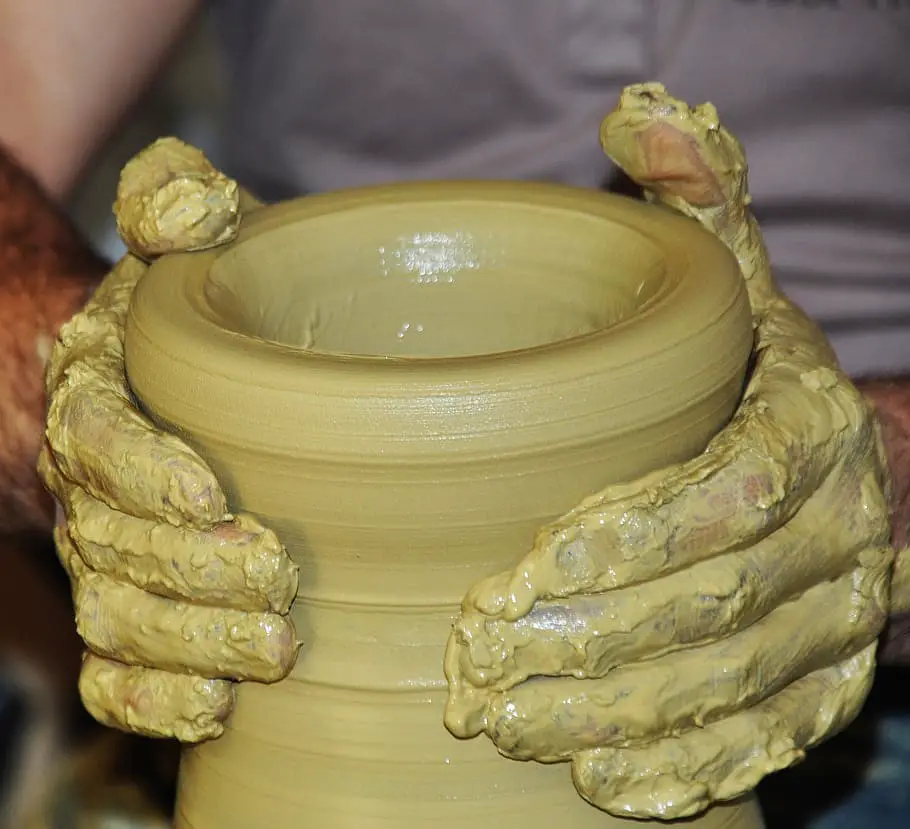
6. Choosing an oven over a kiln:
An oven is a useful tool for the firing of clay if you are working on smaller projects. But, if you are thinking of bisque-firing your clay or planning to fire your glaze in an oven, then you must be clear about the fact that this method is not going to work. The oven is beneficial in case you are planning to adhere some paint onto a pot or design on an initially glazed plate. But one cannot perform firing after glazing or bisque firing in an oven. It cannot reach the optimum temperature required for evaporating the existing moisture from your pottery, locking the glaze onto the surface of your pot, and fusing and fluxing the chemicals to make it food-safe. The maximum temperature of an oven can reach up to 1000F whereas; the average temperature of a kiln is 1200F.
Buying or renting a kiln is a bit costly, and may not be budget-friendly if you are working on small projects for your personal use. But firing pottery using a kiln is the standard and most reliable process of firing, as enough supply of heat speeds up the process, and makes the pottery waterproof, food-safe, and chemical-free. In other words, it completes the project by making it durable and long-lasting. Though you can use an oven if you don’t have access to a kiln, it is always better to avoid choosing an oven over a kiln.
7. Bad firing cycle:
When you glaze your pottery, you might have come across glazing failures like pinholing or dots on your glazed pottery surface. It might happen because of excessive and thick application of glaze, or a wrongly controlled firing cycle. If you are not careful enough about it, your entire effort will be in vain. This phenomenon is not only applicable for firing glazed pottery but also the wrong firing cycle for bisque firing will cause dots and tiny holes on the surface of your pot.
To avoid this kind of problem, set a proper schedule for bisque firing and glaze firing of your pot, based on the process, whether slow or fast.
Here is a firing cycle schedule guide that might help you in your next firing cycle session.
Type | Speed | Hours | Temperature |
Bisque Firing | Slow Bisque | 13 hours | 80F/hr-250F/hr, 200F/hr-1000F/hr, 100F/hr-1100F/hr, 180F/hr-1695F/hr |
Fast Bisque | 10 hours | Increase the rising rate of firing at each step. | |
Glaze Firing | Slow Glazing | 7 hours at 04 Cone | 250F at 150F/hr, 1695F at 200F/hr, 1945F at 120F/hr |
Fast Glazing | Less than 7 hours at 04 Cone | 570F/hr-1695F/hr, 200F/hr-1945F/hr |
8. Not preheating the kiln:
It is a common mistake that beginners commit due to the lack of proper knowledge of the firing process. As we have said repeatedly, the firing of clay is quite prone to risks, and a small mistake can make you pay for it. So, it is always good to become double sure about everything related to pottery firing. As we know, after shaping or glazing the pottery before bisque firing or glaze firing respectively, potters usually leave the clay for air drying to make it dry and hard enough. However, sometimes it is not possible to completely air-dry the pot, as it takes a lot of time. Potters often overlook this factor and pass the partially wet piece into the kiln, which is quite risky.
So, it is recommended to preheat the kiln keeping it at a low temperature of around 180F such that it does not exceed the temperature limit of 212F. Preheating the kiln at this temperature allows the remaining moisture of the clay to get appropriately extracted, thus, lowering the risk of blowing up or explosion inside the kiln caused by the rapid expansion of steam inside the pottery piece. Therefore, preheating is extremely important to save your pot from facing such disasters.
9. Skipping the process of bisque firing:
Bisque firing is nothing but a faster process to dry out your clay to convert it into ceramicware from greenware. Though some of the potters skip this process, we would instead suggest you opt for it, as this technique not only makes the pottery dry faster but also makes the pottery strong and durable enough to work on it further. Also, it ensures that the pottery becomes waterproof.

Skipping bisque firing often leads to the misapplication of glazing compounds. The glaze doesn’t stick onto the surface of the pot well, and the wetness of the glaze may cause the melting of the clay, no matter if it is leather hard or fully dry. Another benefit of bisque firing is that once the clay absorbs heat from the process of firing, it is less likely to react in an unwanted manner when it goes for the second round of firing after glazing. Also, the glaze fits onto the pottery surface properly. So, it is always a smart decision not to skip the process of bisque firing, as it will not only speed up the pottery-making procedure but also increase the durability of the pottery piece.
10. Not following the safety measures:
Last but not least, not following the safety instructions is one of the common mistakes that potters usually make while firing in a kiln. Working with a kiln exposes you to excessive heat and fire, which is quite risky and prone to accidents. There is no substitute for taking the right kind of safety measures while working in such hazardous situations. Often not following instructions leads to major disasters that are impossible to compensate for.
Always stay conscious and attentive enough while working at a kiln. Avoid touching anything right after heating or firing. Let the kiln cool down first, and only then pick up the other things inside it. Always maintain a safe distance while working at the kiln. It is vital not to allow the pottery edges to touch anything inside a kiln shelf. Always keep them at least one inch apart from each other. Cover your skin correctly with fire-resistant clothes and shoes as some extra added safety measures. Always keep patience while working with pottery firing, as a little bit of carelessness is risky for both you and your pottery.
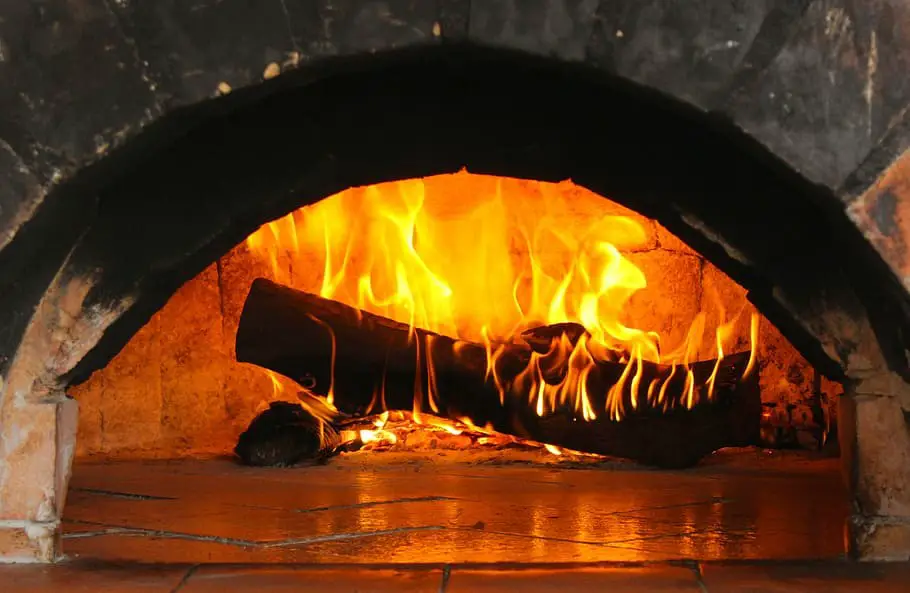
Instructions to avoid dangers while firing in a kiln:
Now, as you know the common mistakes potters make while firing pots, let us learn the instructions that one must follow to avoid dangers and hazards associated with pottery firing in a kiln.
- Avoid touching heating elements while working with an electric kiln as it possesses high voltage.
- Don’t leave the kiln site aloof while firing. Always stay attentive enough.
- Check the ventilation system of the kiln before starting the process of firing.
- While stacking potteries inside a kiln or during unloading them, make sure the power is off, or else it can give you an electric shock and cause other major accidents.
- If there is some unfamiliar or abnormal smell that comes out from the kiln, check its walls properly. If you find anything unwanted, then you must turn off the kiln and look into the matter.
- Change or repair the shelves of the kiln if they are cracked. Otherwise, they may break in the middle of firing, which can cause an explosion and damage to the kiln.
- Do not open the kiln lid unless it is cooled down to normal room temperature. The sudden temperature change might crack your pottery.
- Always keep the cover of the kiln closed to avoid some sort of damage to the kiln wirings.
- No flammable object should be there in the room where you will work with your kiln. Also, avoid placing any object near the kiln, be it flammable or non-flammable.
- Wear safe clothes, shoes, and tinted glasses while conducting the firing process, as looking into the fire directly, may destroy your vision.
- Keep children away from the kiln.
Checking the kiln often
It is essential to know and follow all the necessary instructions for making your pottery. Besides, taking the appropriate safety measures is equally important. But these are not enough to save you from disasters if your kiln is not functioning correctly. You need to check the wirings and internal technicalities of your kiln often to keep yourself away from any vital accidents.
Always measure the kiln temperature to avoid overheating or heat-related hazardous situations. You can opt for thermometers like the Kiln Oven Furnace Digital Pyrometer to measure the temperature of your kiln and get accurate results. It is essential to store the cones with proper care. Right measurements of cones are necessary to achieve adequate firing of your pottery. You may buy Pyrometric Cones For Monitoring Ceramic Kiln Firings that provide accurate results indicating when the firing process is complete.
Conclusion:
Though there are plenty of firing techniques and relevant mistakes to talk about, these 10 are the major ones that people often make that lead to failure. So, if you are a beginner, learn the proceedings first, and then go for firing your pottery while following the proper safety measures. It is always good to experiment with techniques and tricks but keep the danger factor in your mind before experimenting. We hope that these tips will help you avoid major pottery mistakes and aid you in making marvelous and unique pottery pieces. Happy sculpting!