You’ve probably fired some clay in the past. But, did you know that different things happen when you’re firing it? It goes into different stages, and depending on how the clay is fired, it does affect the overall outcome of the clay. This post will discuss the different stages of firing clay, and even what happens during all of this. It’s unique, and you’ll learn just what happens to clay when it is fired here.
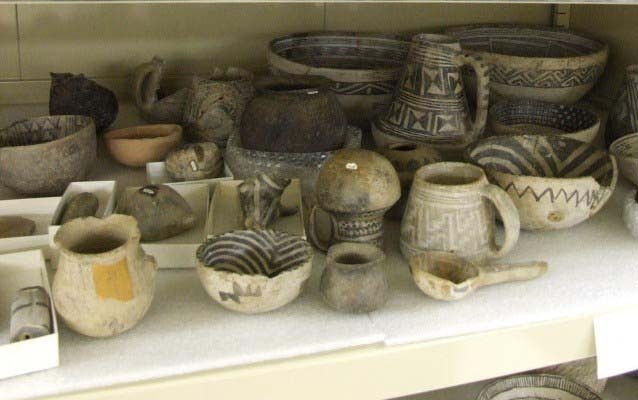
Air Dried clay
The first thing that you’ll want to look at is air-dried clay, which of course is clay when it’s dried by air. When this happens, the following occurs in this.
- The particles in the clay come together
- Water starts to evaporate from this, and it causes it to shrink
Typically, if you form the clay in certain ways, and it starts to be uneven when it dries, this can affect it and cause clay stress. If you do notice this, it usually happens when the stress shows up as cracks, or even as warpage, and in other cases, you may not see this right away, but it happens when the firing occurs. So, you want to make sure that it’s dried evenly, to give it a uniform thickness, and it’s important to make sure.
Most of the time, clay that’s very fine shrinks more than those with larger particle sizes. Porcelain is very fine, but it also shrinks the most. Those that are dry tend to have the most strength, however.
If you have a groggy sort of piece, it tends to shrink the least. That’s because of the following:
- The grog has already been fired before to various sizes
- It tends to have lower content, to begin with
- There tend to be more channels for the moisture to get to the surface
When the water is evaporated from this, the rest of the pieces shrink. you’ll notice that before you throw it into the kiln, it goes through the leather hard stage, which in essence means that the particles are damp, but it won’t shrink anymore due to already having shrunk enough.
The Atmospheric Drying Stage
Let’s discuss this first stage. This is when the pottery is put in the kiln, most of the time bone dry, but some clay has water between the spaces, and it’s important to have these particles here
.
Now as the clay heats up, the following happens:
- Water evaporates from the clay
- Compacts a little
- May shrink a tiny bit
However, one thing to know about this is that if it is heated up too quickly, the water will begin to become steam, and from there, it expands and creates something explosive to the pottery itself. However, if you are able to make it so that it hits the boiling point easily, you’ll be able to ensure that you do this correctly.
Most of the time, you want to slowly get the kiln to this point, because too fast will shock the pottery piece itself, creating problems later on because of this.
The Second Stage
This is a point that’s reached somewhere between 572-1470 degrees where the clay bodies start to burn off some of the organic compounds. These include the following:
- Carbon
- Organic Materials
- Sulfur
if for whatever reason they’re not able to release this, such as in the case of the kiln having poor ventilation, then you won’t be able to burn out the body of the clay, and then the following will happen to it:
- Carbon coring
- The clay body weakens
- Could completely sacrifice the overall look of it
That’s why it’s very important to ensure that your clay body has the correct amount of ventilation while it’s in the kiln. It does affect the overall state of the body itself and can make a big difference in the full product
Stage Three
At this point, you are going to drive off the chemically combined water. What this means is simple. let’s take a moment to discuss what clay consists of. Two elements play a part here and they are as follows:
- The two molecules of silica
- The two molecules of water
- A molecule of ammonia
These are the main factors, and now, even after the clay is leather-hard and most of the water is gone, there is still about 14% water on this chemically bonded per weight. You’ll notice that when this happens the clay body won’t shrink, but it becomes lighter and it often is what results in the typical piece that you know about.
Usually, at this stage, the water that is in this has crystals within it, and these tend to escape when you single fire this. Typically before this, most of the bound water that is itself between the mineral and clay particles gets pushed out. However, when you have water bound into the crystal of the clay itself, and the other minerals in this, you’ll start to notice that the weight gets lost at this point too.
It actually can be affected in other ways. For example, while some lose about 2-4% of water, kaolin porcelain can lose about 10% of the weight itself due to this crystal water. Calcium carbonate, when used, actually loses about 45% of its weight. It’s a good thing to learn a bit about this because this stage has a range of temperatures so it can happen here, or potentially earlier. Because there are large amounts of water generated, it’s important to ensure that you don’t push the kiln super fast. Doing this is a slow process. Remember, you want to make sure that you keep in mind the “ceramic change” that is happening. Changes occur, so make sure that you understand this.
So should this be a concern? The answer is something that you need to choose for yourself. There are a few concerns that happen during this point, and they are as follows
- The pores within this have channels that allow steam to come out
- While shrinkage does happen at times, the ware is fragile due to the lack of particle bonding that happens
- You may want to make sure that you have the piece ventilated again so that you can get rid of the chemical steam that’s happening from these bonds
Now, when you heat this, the bond between this in the water and the other chemicals starts to loosen up. Remember, by this point, the carbon and the sulfur burn off from here, and the bonded water does escape from the clay at this point somewhere between 660-1470 degrees Fahrenheit. If you notice that the water starts to heat up too quickly, this is also a problem, because of the following:
- You get too much steam built up in here
- This can result in an explosion of the clay body itself
If you do this, make sure that you have a firing schedule that does provide the ability to slowly build the heat so that it doesn’t deter the full product, and furthermore risks the explosion that could come from this if it is heated up too fast.
Stage Four
This is a stage known as quartz inversion. So what is quartz? Well, in essence, it’s often known as silica to the average potter, but you can also call it quartz.
Quartz or silica has a crystalline structure, and this changes at different temperatures. When it does this, it’s called an inversion, so in essence, this is the change that happens to the pottery at certain levels.
This typically happens around 1060 degrees, but the change is a good thing. Do you know why that is? That’s because of the following:
If you do have this stage happen, you need to make sure that you slowly raise the temperature in this. The ware is fragile due to this stage, so you always need to take your time. That’s why kiln firing is such an in-depth and long process. Because if you do it too fast, then it causes problems.
Decomposition
This is a stage that typically happens in between this, and it mostly happens with feldspar and kaolin more than anything. In essence, you’re deconstructing these two elements into more chemical forms.
Here are a couple of ways this can happen:
- Kaolin crystals become mullite crystals
- The reaction temperatures happen without this melting
- However, when feldspar melts, the particles start to go faster, and it does make the process much quicker as well-being
- Typically at this point when it deconstructs, it lets out carbon dioxide and sulfur.
If you hit this stage, these two elements must have a means to escape, because if not, it can cause explosions or even more issues with the overall state of the particles. Many times, when the firing continues, the glaze materials melt into oxide blocks, and sometimes, the deconstruction bubbles up through a molten glaze. If you have especially transparent glazes, you’ll notice that these actually will bubble up because of this. It’s important to watch for this if it’s vicious, or it’s got high surface tension.
Usually, this reconstruction happens when oxides and particles change begin to happen.
Now, when the temperature does drop, either by soaking or shutting off, the decomposition stops, and the recomposition does begin. It’s quite interesting when it starts to cool off, and we’ll go over cooling off later on too since it’s a very important step. At this stage, the following tends to happen:
- The glaze that’s normally on there is oxide molecule arrangements
- It does require extensive time to crystallize and form
- These particles and melted glass start to move altogether.
Stage Five
This is called sintering. Now, before the oxides that make the glass start to melt, the particles in the clay start to stick to one another. Typically, at around 1650 degrees, the particles will start to fuse. The sintering is usually something that it does on its own, and this is very important for the pottery because this in essence how the shape is created. This fusing process allows for the glass to become the best form that it can be, and the clay must reach this stage.
Now, if you choose to bisque fire this, you need to crank up the temperature to about 1730, but don’t go any higher. That’s because if it does, the following happens:
- It’s porous, but not vitrified and completely matured
- It allows for the raw glazes to adhere to your pottery without it breaking down
So, if you do the bisque fire, you’ll want to crank the temperature to around this, and make sure that the clay has enough time to fuse, but also not enough time to completely vitrify and mature.
Stage Six
This is the stage of both vitrification and maturity. Vitrification, in essence, is the melting that allows the body to become hard and durable, and it’s important to make sure that you do this. However, you have to make sure that you don’t have too much to happen.
If it’s too little, the body will start to suffer, but if it’s too much in terms of vitrification, the following tends to happen:
- The body will start to deform
- It can start to slump and fall at an angle
- If it’s too much, it completely melts and becomes a puddle on the shelf itself
This is a very gradual process, so you need to make sure that you don’t take it too fast. You want to make sure that the materials that melt the easiest have enough time to do so. During that, the rest of the spaces have refractory particles thrown into them. The particles that melt do create further melting, so it does help with making the clay body stronger.
You need this, but you need to also remember that if you do take this too far, it can end up causing the entire body to melt as well.
Another element that happens during this stage is that something called mullite is formed. This is an aluminum silicate, and these are in essence crystals that are binders that pull everything together and make the clay body a lot stronger. They create a sort of knitting motion, so it’s important to have this happen if you do end up liking the result of this.
The Temperatures
Now, where you fire this makes a huge difference in the overall result of this. For example, if it’s fired to only one stage, you’ll get it in a state that’s both porous and soft, but then, at a higher stage, it’ll be impervious and strong. You should make sure you also limit how high the firing is when you’re doing a bisque. This gets up to around 1700, but any further it can cause maturation, and in turn, it can cause the clay body to not want to accept the glazes you’d like to put in.
But, you also need to look at the type of clay that you’re using too. It’s important to realize that clay does have different maturation temperatures. For example, if you have clay that’s got a lot of iron, this does create a flux in this. Here are a couple of different elements that you should remember when looking to fire the clay body:
- The earthenware clay body fires to maturity at 1830 degrees and melts at 2280, so you have to keep it around there
- Porcelain, since it doesn’t have any iron within it and is made of kaolin, may not mature until it hits 2500 and doesn’t melt until it’s about 3300 degrees. That’s super hot, and you’ll want to make sure that you watch how high this gets. Porcelain tends to take a bit longer as well, so keep that in mind when you’re looking at the different temperatures.
The best thing to do, if you have a question about the maturation temperatures of this clay, is to look online, or at other research, to see what the best temperatures are. To fire the clay is. There are a lot of factors that go into this, so make sure that you fully understand yourself when you’re looking to get the most out of this.
Reduction
For those that are in the industry, a reduction is a common thing, used to achieve various effects, including the following:
- Earthy brown colors
- Copper red glazes
It’s something that many people do if they know how to fire pottery because the idea is to give only a little bit of oxygen to the kiln to burn the kindling in there. Some people do even less of a reduction, which causes unburned carbon to come into this
Typically, this denies the iron within its oxygen as it would normally have, and this creates a reduced form to create the desired colors. It usually is done around 1000 degrees, and then it’s brought up to the melting temperature in a neutral state, where it’s done once again to reduce it to the colors that you want from this. Some people will have a small period of oxidation to get rid of the carbon on this. This is a good one if you want to try out firing and have the element of mystery attached to it. However, this often creates a very unstable atmosphere, so you need to be very careful when you’re doing this. It’s a type of atmosphere that should be followed to a T by instructions due to the dangers of this.
Cool down
This is an event in it, and it’s worth mentioning. It’s an event where the clay does cool down, and then it causes shrinkage of the element called cristobalite, which is crystallizing silica, and as it gets all the way down to 420 degrees, you’ll be able to cool this slowly once it gets to this temperature.
You always want to cool this slowly, because the following tends to happen:
- It will be weak otherwise
- It will develop cracks
- It can end up ruining the integrity of the pottery itself
It’s important to make sure that you do this slowly since this will cause the crystallization to happen. If you notice that there is an undesired level of crystallization happening, you should adjust the glaze of the chemistry itself, and from there, speed up the rate of it dropping during this change. Be smart with this, and if there is glass on there, you’ll want to make sure you take good care and ensure that you get good cooling after the firing happens.
Firing has a lot of different processes and actions that it entails. By ensuring that you have this all in place, and understand how you can fire them, you’ll be much more successful, and get a great result from this. Start to learn how to fire the clay today, and know how the different temperatures affect the overall state of the clay. It’s important because this is how you maintain the temperatures and know exactly what is going on with it as this transpires. Learn how to do this, and learn how you can adjust the temperatures as needed to create beautiful pieces that work wonders for your pottery adventures and whatever it is you wanna make.