If there is one thing you need to know as a potter, will be terracotta. Terracotta is popularly known as “cooked earth”. It is also known as red-burning earthenware. Terracotta has been made for thousands of years by indigenous cultures, most often unglazed. If glazed, high lead content mixtures have been traditional. According to Wikipedia, Terracotta is a type of earthenware; it is a clay-based unglazed or glazed ceramic, where the fired body is porous. Terracotta is the term normally used for sculpture made in earthenware, and also for various practical uses including vessels (notably flower pots), water and wastewater pipes, roofing tiles, bricks, and surface embellishment in building construction. The color of most terracotta pieces is a natural brownish-orange color which varies considerably.
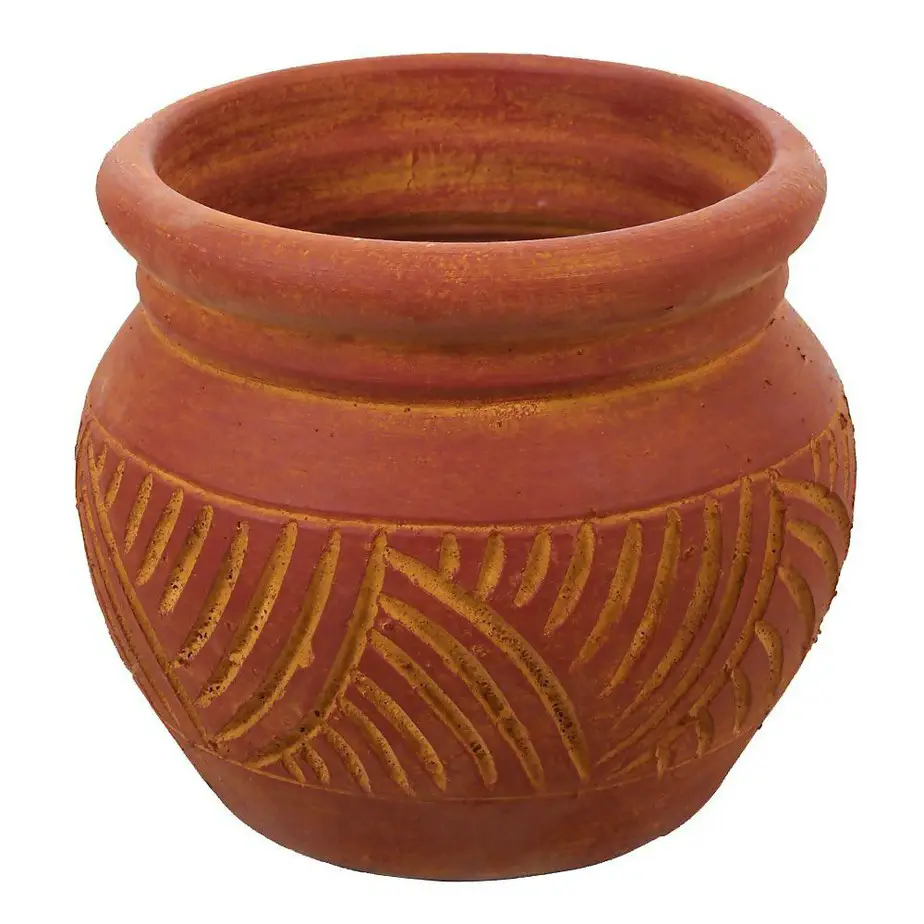
WHAT IS TERRACOTTA?
In archaeology and art history, the word “terracotta” is often used to describe objects such as figurines that are not made on a potter’s wheel. Various vessels and other objects that are or might be made on a wheel from the same material are called earthenware pottery; the choice of the term depends on the type of object rather than the material or firing technique. Glazed architectural terracotta and its unglazed version as exterior surfaces for buildings were used in Asia for some centuries before becoming popular in the West in the 19th century.
Terracotta is often used in industry to make sculptures, vessels, pottery pieces, tile, planters, gardens, and architectural ware. When terracotta gets glazed, it is preferably called ‘red earthenware’ rather than ‘terra cotta’. It is no accident that terra cotta fires red (although the actual raw clay can be brown, maroon, green, or red). Red-burning low-fire clays are available almost everywhere. They are almost always very impure, contaminated by a range of fluxing-bearing minerals and iron oxide (which produces the red-fired color). The contaminants act as fluxes, making the material fire much harder than would a mix of white burning clays at the same temperature. Engineers refer to the degree to which a lump of clay has been fired as its “maturity”. You can always get your terracotta clay for less than $17 on amazon by clicking here.
Achieving a crystal-clear, durable, defect-free, non-crazed glaze surface on terracotta is not easy. Often terracotta glazes have poor working properties (this means that they settle quickly in the bucket or turn into a jelly that is difficult to apply). Success is achieved with a combination of the right chemistry to produce a good glaze, the right recipe, mixing, and gelling procedure to produce good working properties, the right bisque temperature, application technique and the right firing schedule to melt and level it well.
Ideally, you should buy your terracotta clay from someone that can provide support for the entire process. Buying it as a kit with the slip, glaze, colors, and instructions all included is even better. If you can make it work well you could spend a lifetime with the process!
As I mentioned earlier, the color of the terra-cotta will vary drastically depending on the color of the clay used. Terra-cotta items can be coated with a glaze to make them look brighter and help preserve them. Glazing terra-cotta products require access to a pottery kiln.
HISTORY OF UNGLAZED AND GLAZED TERRACOTTA
Terra-cotta was first invented in the pre-historic age and used as the only art for sculpturing. Historians and Archeologists have found many terra-cotta showpieces, utensils, kilns, statues, etc. of various times and periods, starting from the pre-historic age. The preliminary stages of terra-cotta were unglazed.
The unglazed terra-cotta potteries were used for many ages, and gradually the art got spread out all over the world in various civilizations like Mesopotamian, Egyptian, Chinese, Indus Valley, Greek, and many more. With time, this terra-cotta art got improvised, and new methods were created for making various kinds of terra-cotta pottery pieces. These terra-cotta pots were used in every field at that time.
The Greeks developed fired unglazed earthen pots and utensils in the 5th century BC. They used them for storage purposes and cooking. The terra-cotta items of that time were quite porous and couldn’t hold water for much time. Later on, in the 1st century BC, Egyptian people developed glazed terra-cotta potteries, which are widely used today’s date. They first prepared a blue-green glassy glaze, which was used to apply on the terra-cotta pieces. This glazing mixture is commonly known as the ‘Egyptian Paste’ and is still much popular in the world of pottery.
Apart from the Greeks and Egyptians, terra-cotta art is also prevalent in Chinese civilization. Glazed Terra-cotta potteries were widely made in early China and the Middle East at that time, and were traded along the Silk Route. Many great sculptures of unglazed terra-cotta were built during these ages.
After the introduction of glazed terra-cotta pots, which were more efficient and beneficial, the art of glazing spread widely. In the Medieval period (during the Renaissance period), many famous terra-cotta sculptors engaged themselves in formulating innovative ways to create glazed terra-cotta pieces for the increasing usage of terra-cotta clay. The glazed terra-cotta potteries had also become an important feature of African sculpture at that time.
In the 18th century, in England and America, unglazed terra-cotta began to be used in architecture. Later on, in the 19th century, glazed architectural terra-cotta was introduced for wall and floor constructions.
TYPE OF GLAZES
Let us talk about the type of glazes before we move into how to glaze terracotta pieces.
1. Earthenware Lead-Free Glazes
This is designed to be food and drink safe and there are a large number of colors and special effects to satisfy all tastes. It contains minimal elements of lead, making it very safe to use to eat/drink. Many potters use this type of glaze when crafting dinner wares.
2. Earthenware Glazes Containing Fritted Lead
This type of glaze contains a significant amount of white and/or red lead. Thereby it will be toxic if used in the making of dinnerware. This type of glaze is mostly used to decorate and coat flower vases. Some companies use a lead bi-silicate frit which is a combination of materials melted together to render them insoluble and resistant to acid attack. Lead bi-silicate frit, therefore, is a means of introducing a material that will render the white/red lead anoxic.
3. Stoneware & Mid-fire Glazes
All these glazes are very constant under both dissolving and reducing conditions. Very many variations of color and properties can be produced by using different colored and stippled bodies. All of the glazes are inter-mixable, allowing unique double-dipping, mottling, and pouring on or painting on of different glaze colors/types over or under another glaze color/type.
4. Raku Glazes
Raku glaze is any glaze that is being used in the Raku method. Raku is a type of Japanese pottery traditionally used in Japanese tea ceremonies. Raku glazes are often fired at low temperatures. The fired raku piece is then removed from the kiln and allowed to cool in the open air.
HOW TO GLAZE TERRACOTTA PIECES?
Below are some useful tips that will guide you in glazing:
1. Chose the right terracotta project and the right glaze
The selection of glaze is one of the most important steps to creating a masterpiece. Before you select a glaze, you have to make sure your piece has gone through thorough firing (bisque firing). If you have a clay object you made yourself, fire it in the kiln to make it hard but still absorbent before you glaze. The temperature of the fire is determined by the type of clay you use.
Most times, I advise beginners to purchase a premixed glaze or they should get their glazes mixed by a professional due to the chemical compositions involved. The firing temperature and the components of the glaze should also be considered when choosing a glaze. Don’t use two glazes that require different firing temperatures.
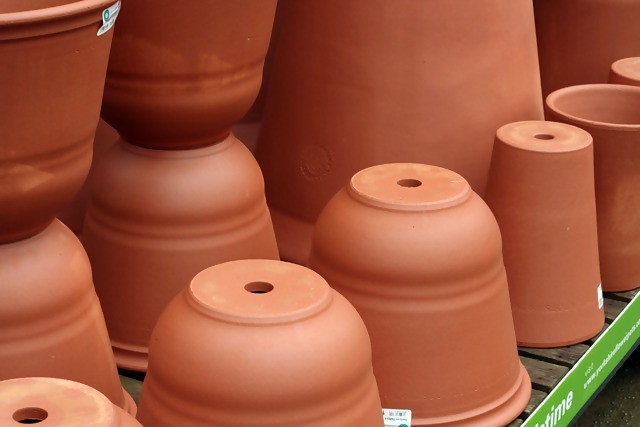
As I advised above, you should always get a premixed glaze if you are new to glazing. You can always order your premixed glaze by clicking here.
2. Prepare the project and the glaze.
Use sandpaper to rub the surface of your piece properly. If you see bumps on the object that aren’t meant to be there, you should sand them off using 100-grit sandpaper until you have a smooth surface all over your piece. Clean the piece after sanding off the bumps. Then get your project a little bit wet and clean by using a damp sponge to wipe the surface of your piece. Also, apply wax wherever two removable parts meet, for example, a mug and its handle. The wax should be applied with a separate brush. As earlier stated a pre-mixed glaze is highly recommended for your first few projects due to the safety hazard and difficulties that will be involved when mixing your glaze. If you decide to mix a dry glaze powder with water, be sure to follow the manufacturer’s instructions carefully, or else your glaze may not be according to your desire. Remember to always wear a mask when working with glazes.
3. Apply the Glaze on your project:
Before you apply your glaze, it is advisable to stir it well even if you are using a premixed glaze. After you are done mixing the glaze, keep each glaze separately with its brush. Separate brushes for each glaze to make sure glazes don’t mix. Decorate your project with brushes dipped in underglaze. You can get creative with it by flicking the brush or making twirls and twists. It depends on you. After a while, you can apply your overglaze by brushing the glaze onto the project or dipping the piece in an overglaze for about 1-3 seconds. Be careful with your glazes, too many glazes can ruin a masterpiece.
Below are a few ways to apply the glaze to your terracotta project.
METHOD OF GLAZING | RATINGS (OUT OF 10) |
Brushing | 7. Brushing is not as complex as other methods and there are limited complications. |
Spraying | 6. It is recommended if you are applying Overglazes |
Dipping | 9. This is the most popular method of applying glaze on pottery although it might be a little bit complicated |
Pouring | 5. This is mostly done for the interior of the glaze. If not careful, you might ruin your project. |
METHODS OF APPLYING GLAZE ON TERRACOTTA
Brush the glaze on your terracotta
Many ready-to-use glazes are being sold. These glazes tend to be much thicker. Some are a little less fluid than heavy cream, while others are so thick as to be pudding-like. Make sure you read the instructions carefully, as they will tell you how many coats to use for your desired color. Since these glazes are thick, it is easier to brush on your piece. Synthetic sables are the best brushes for brushing glaze on a terracotta piece. They are durable and be reused anytime. Kindly wash your brushes fully after using them on a piece to prevent bacteria.
Spray Glaze on Pottery
Spray guns and airbrushes are two tools potters use to spray underglazes and overglazes onto their terracotta. Spraying is recommended when applying overglazes on a piece. Care should be taken on several counts when considering this option. Spraying Glaze should be done in a well-ventilated area. A NIOSH/MSHA-approved face mask or respirator should be used when spraying glazes on ceramic.
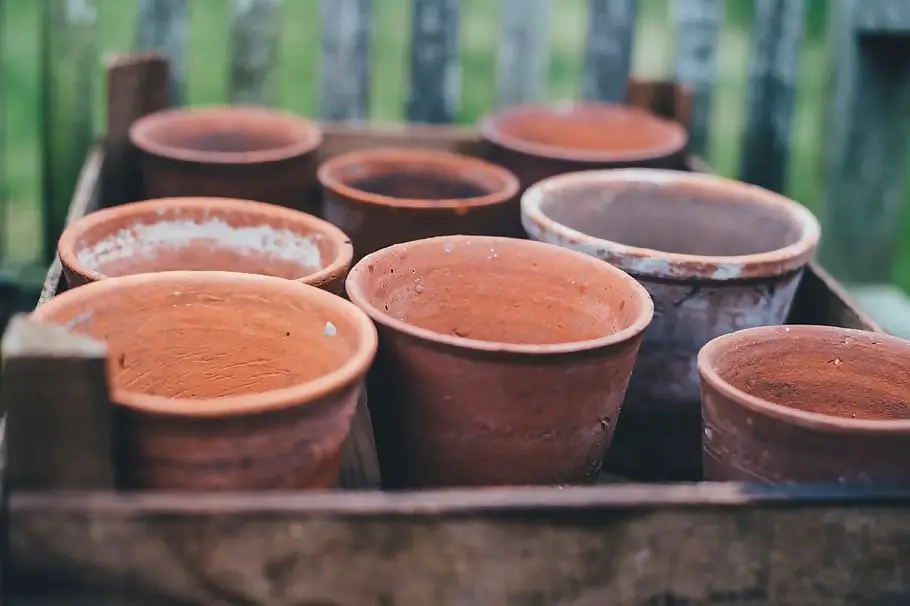
Dip pottery into the glaze
This is the most popular method of applying glaze on terracotta pieces. The pottery is immersed in the glaze for about three seconds to six seconds. This is one of the fastest ways to glaze large quantities of ceramic pieces. It also is a good method to ensure an even glaze coat. Make sure the glaze has been prepared properly and stirred thoroughly (make sure there are no air bubbles). I usually advise pottery beginners to get a premised glaze instead of preparing a glaze themselves as it involves some technical measurements and components.
Pouring glaze
This is usually done along with dipping glazes. Dipping is for the exterior while pouring is for the interior. To glaze interiors, glazes can be quickly poured into the terracotta art piece, left for three to five seconds, then quickly poured back into the glaze bucket. Glazes can also be poured over the exterior surfaces of the piece.
4. Fire your Glaze
To make your glaze stick to your project for life, you will need to fire your glaze. Make sure you fire the glaze according to the recommended temperature. Glazes are either low-temperature or high-temperature and firing them at the wrong setting may cause your project to break.
The above procedure might seem too voluminous for you to do. Here is a simplified way to glaze your pottery.
Step 1: Fire the terra-cotta item in a kiln at 1700 degrees Fahrenheit or hotter. The temperature of the kiln can be adjusted depending on the type of clay being used.
Step 2: Make sure you fill a pan with paraffin wax and heat it until the wax melts. Dip the base of the terra-cotta object in the wax to prevent the glaze from fusing it to the kiln shelf. If the item has a lid, brush the wax on the areas where the lid meets the base.
Step 3: Fill a container large enough to submerge the object with glaze. Glaze can be purchased from local craft stores or it can be made by hand.
Step 4: Hold the object with a pair of dipping tongs and fully submerge it in the glaze. Pull it out and allow most of the glaze to drain back into the bucket.
Step 5: Set the object on the newspaper and allow the glaze to dry completely.
Step 6: Fire the object in the kiln between 2100 and 2300 degrees Fahrenheit for 16 to 18 hours. The exact temperature and length of time depend on the kiln and glaze, so some experimentation is necessary.
Step 7: Allow the terra-cotta item to cool in the kiln for 24 hours and remove it.
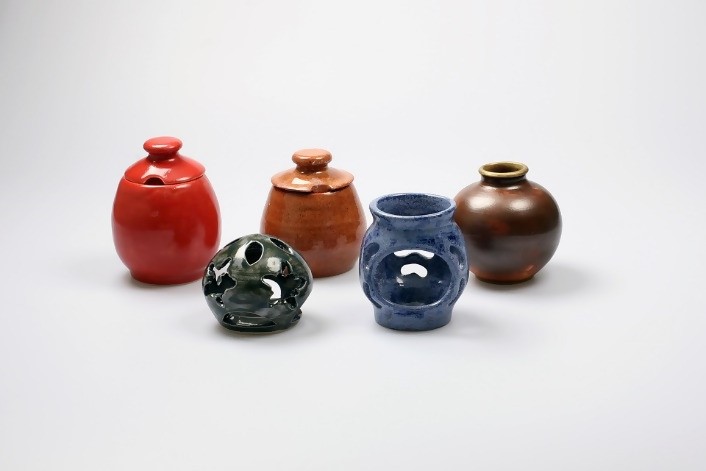
Whether your project is a tiny terracotta mug or a large vase, glazing is still an essential aspect of the pottery process. In this article, I have explained the types of glazes you can use to glaze your terracotta pieces and lastly steps on how to glaze your terracotta projects properly.
TOOLS USED IN GLAZING TERRA-COTTA POTS
I have already explained the basic facts about terra-cotta clay, its sculpting, and the process of applying glazes to terra-cotta showpieces. But, do you know what tools or equipment are used for applying glaze on terra-cotta pots?
Well, here, I have given a table in which you can get to know about the tools used in making Glazed Terra-cotta pieces.
TOOLS USED | FEATURES AND USES |
Kiln | Glazed terra-cotta potteries are fired in the kiln. It is a furnace made of non-inflammable material to fire clays. It works with the help of electricity or gas. |
Fettling Knife | This knife is a kind of tapered tool, which is used to trim clay and give shape to glazed terra-cotta sculptures. |
Modeling Tools | These tools are extensively used in trimming, shaping, decorating, and giving textures to terra-cotta pieces. These tools do many excellent designs on the body of the pots. |
Glaze Brush | Brushing is an essential step in making glazed terra-cotta items. These particular kinds of brushes are used to apply glaze on the clay body. |
Glaze Mixer | Like all the other manual mixers, the glaze mixer is specially used for mixing glazes well, before applying them on the surface of the terra-cotta clay pots. It has a rotating sieve with a handle for easy mixing. |
Glaze Sprayer | This tool is used for giving finishing touches. The sprayer is filled with glaze and sprayed onto the body of the terra-cotta piece after the glaze is applied manually. It is also used for spraying glaze on the missed out parts. |
ADVANTAGES OF APPLYING GLAZE TO TERRACOTTA POTTERY PIECES
So, the next thing that you must be wondering about is the benefits of applying glaze on the surfaces of earthen terra-cotta pieces. Well, in this section, I have highlighted the advantages of using glaze on terra-cotta clay bodies. Have a look.
1. Retention of moisture:
One of the significant differences between glazed terra-cotta and bare terra-cotta pots is the moisture-retaining ability. This feature is present in glazed terra-cotta pots more than the normal ones. Glazed terra-cotta items hold enough moisture from outside, keeping the interiors cool. And this is one of the reasons why most terra-cotta utensils are glazed.
Terra-cotta is burnt at extremely low temperatures, which makes it susceptible to freezing. The scientific logic behind increased water retention of the glazed terra-cotta products is the reduced cooling effect. This effect occurs because no evaporation through the item’s walls takes place, and also the walls are not gas permeable.
2. Repellence of water:
After glaze application on a bare terra-cotta pot, the product becomes a great water-repelling substance. The body of the pottery is made waterproof by applying a glaze coat on it. After undergoing the intense process of glazing, when the body of the terra-cotta item cools down, and its outer surface turns into a smooth and solid surface, then this glazed exterior results in becoming a tight surface, which is impervious to water. It also holds liquid for a much longer time.
However, glazing on the terra-cotta pots tends to fade and shrink eventually. So, taking care of the glazing is indispensable to coordinating the expansion and shrinkage rates of the glaze.
3. Increases strength of the terra-cotta piece:
Another crucial feature of glazing is adding strength to a pot and delivering the ability to protect it from hazards. The primary advantage of glazing a terra-cotta piece is that the glaze provides additional strength to the outer body of the clay piece. By glazing, a regular terra-cotta item can be transformed into a smooth yet robust product.
Glazing also strengthens the clay composition of the pot. Potters usually calculate the glaze fit, the relationship between glaze and clay composition. When they craft a glazed item following the glaze fit, the burnt glaze fits tightly on the terra-cotta surface. This process compresses and holds the clay molecules tightly bound, thereby making the piece stronger.
4. Long-lasting advantage of glazed terra-cotta:
The advantage of the durability of a glazed terra-cotta item comes from the strength that the glaze offers to the terra-cotta body. However, it is evident that a terra-cotta showpiece, be it glazed or unglazed, is very brittle and delicate. So, it must be handled with care.
Now, keeping aside accidental harms like sudden falls from a height or disorganized handling, if we look into the matter as the basic durability of a substance, then glazed terra-cotta is very long-lasting. As said before, compression causes tightness of clay molecules, which gives a hard nature to the pottery body. This compression factor also increases the durability of the material.
5. Suitable for decoration:
The glazing of terra-cotta surfaces gives it a smooth and beautiful outlook along with a sleek and glossy finish. People always find them very attractive and catchy. They buy and decorate terra-cotta items in their house. Both overglazing and underglazing of terra-cotta pieces provide a decorative outcome. They come with a variety of unique designs.
Apart from decorative glazed terra-cotta showpieces, glazed terra-cotta tiles and building stuff are also crafted. Nowadays, glazed terra-cotta pottery is majorly used in forming architecture in various countries. The reason behind it is mostly the strength and water retention ability of glazed terra-cotta.
USAGES OF GLAZED TERRA-COTTA
Glazed terra-cotta pottery has extensive uses in our daily lives; let us know some of its important applications as listed below.
-
Glazed terra-cotta pottery as earthen materials:
Glazed terra-cotta is an age-old invention, which is still now prevalent for satisfying various purposes. Previously, it was mainly used for household and trading purposes. Glazed terra-cotta earthen materials like utensils, statues, and showpieces were made by ancient people to earn their living and also for personal use.
-
Glazed terra-cotta as utilitarian substances:
Terra-cotta is prevalently used in crafting potteries for utilitarian purposes. Many utensils are made out of terra-cotta to serve household purposes. Thus, terra-cotta is used in making several utilitarian objects like flower pots, water pots, and vessels for food and grain storage. This type of clay is also used for making water and wastewater pipes, roof tiles, bricks, and surface embellishments.
-
Glazed terra-cotta as ornaments:
Terra-cotta is also used to make ornaments and jewelry. It is now effectively used in making smoke pipes, bangles, necklaces, and earrings.
-
Glazed Terra-cotta as varieties of architectural designs:
With time, glazed terra-cotta found its implementation in the creation of architectural wonders. It is a ceramic masonry building material that is used as a decorative outer layer. In the late 19th century, this art in architecture became quite famous and the most common building material in the U.S. Both glazed and unglazed versions of terra-cotta are used in architecture because they are sturdy and cost-effective.
The glazed terra-cotta, due to differences in burning, causes variations in textures and patterns, which make them look like granite and limestone. This creative pattern and design attract many architects to use terra-cotta clay. There are four major types of terra-cotta used extensively in architectural buildings.
Glazed architectural terra-cotta is the most complex building material. It is used in making strong walls of buildings, ceilings, pillars, and roofs of houses.
CONCLUSION
Reaching the end of this article, I can conclude the fact that Glazed Terracotta is a huge invention in the world of sculpture. This art has had a significant impact on the culture of various countries. Keeping into account the beginning of terra-cotta usage that dates back to the beginning of human civilization, it has been widely used. And still, now, it is being used in the construction of various sculptures, be it a building, statue, or earthen utensil. So, with utter expectation, to maintain the tradition and culture of humanity, the art of glazed terra-cotta must be preserved and kept alive by continuing its uses. Passing on the knowledge of this art to future generations is also to be counted.