The world of pottery making is simply superb with its rapture and creativity. Not only the entire process of pottery making is fantastic but also adding glaze to the pot gives a whole new life to it.
The application of glaze does not come in the form of decoration for your pottery, but also it is a great way to add more strength to your pot. It creates a coating over the porous surface of the pottery and makes it pretty durable and useful.
What is more interesting about glazing is that it comes in a brilliant and fantastic variety. Various glazing techniques come with their unique process and appeal. Also, each of the glazing methods includes a difference in their technique, which renders them more unique characteristics. One such fantastic glazing technique is raw glazing, which is unique and different.
So, here is what you need to know about it.
What is raw glazing?
When it comes to glazing, the basic idea that comes to our mind is the application of water-based glazing after bisque firing the greenware. It is usually done to ensure that the clay pot does not go back to its muddy form while applying the glaze.
On the other hand, raw glazing refers to applying the glaze on the pottery body without opting for a single firing before the application.
It involves applying water-based glaze to the semi or completely-dried clay which is immediately going to dissolve. Then it is fired. This method is called the single-fired process, which involves only one firing in the entire process. Usually, the raw glazing process does not include the biscuit firing before the glazing.
While the preliminary firing process sounds quite a bit safer for others, many prefer to opt for raw glazing as it renders a unique look to the pottery project. Also, it is a common technique, that has been in play since the 17th century.
Here is a comparison between single-fired pottery and bisque-fired technique.
Factors about glazing | Bisque fired glazing | Raw glazing |
Ease of making | The bisque-fired glazing takes much time, as you have to go through the double firing process. | Raw glazing requires only a single firing process after the final application of the glazing, which makes the process easier. |
Strength | In the case of strength, the bisque firing process is more reliable as it makes the clay baked and hard. | In raw glazing, there is a risk of the clay becoming soft during glaze application. |
Ease of application | Applying glaze on bisque-fired pottery becomes tough with the brushing technique. On the other hand, the dipping process becomes easier for application. | Spraying and brushing become much more reliable for raw glazing, while the dipping technique can be difficult and risky. |
What are the advantages of the raw glazing technique?
It sounds a bit difficult as there are chances for the clay to become mud without proper handling. However, it comes with many advantages, which can make you feel that it is worth trying. So, what benefits does it offer?
It includes lower efforts:
Though it is quite a bit difficult, it does not require much effort to prepare. Usually, it involves less process since it eliminates the preliminary processing. Hence there is no need to fire it more than once. Thus, it helps you to have less time and involvement in your entire process.
Time-saving:
While working with the raw glazing process, there is no need to wait for a long time to dry out the pottery. You can apply the glazing when the pottery is semi-dry, as the water-based glazing will sit on the pottery’s surface properly.
Easy to obtain even thickness while glazing:
When it comes to glazing the bisque-fired pottery, it tends to become more absorbent, making it tough to apply the glazing all over the pottery body in a much even way. It can make the glaze turn out to be very patchy and tough to tackle. In contrast to it, glazing on the greenware comes with a less absorbent texture where it is easier to apply a very even coat.
Easy to add nicer effects:
When you use a brush to create more creative effects for the glazing, it can be difficult enough to work fluently on a bisque-fired pottery body. On the other hand, the raw glazing technique is much easier to apply as the fluid on the greenware tends to stay for a bit longer. Hence, you can mix the glazes over the surface with brush strokes.
Works better on high clay content:
When it comes to working with the high clay content glazing, it becomes easier to deal with it on greenware as it tends to adhere appropriately to the clay body and makes it look much good after firing.
Includes lower energy usage:
When it comes to the raw glazing process, it is more energy-saving. It is going to include a single firing process. With only one final firing, you can have completely glazed pottery, which lowers the energy usage of the double firing. The kiln exposure is going to be for a single time which is much energy saving.
Environmental-friendly:
Firing pottery two times is going to be the reason for the emitting of gases. Thus, single pottery firing sounds more convenient as it will involve less carbon and other gas-emitting than the two times. Therefore, looking for this way of pottery making is much more reliable than the other ones.
How to ace perfect raw glazing?
If you are thinking of trying out the raw glazing technique for your next pottery project, it is essential to use the proper tricks and techniques. Here are some of the tips for you:
Pick the right clay:
When it comes to the raw glazing for your pottery, it is vital to ensure that it has a suitable clay surface. The clay needs to be much stronger for this one. Choose a clay that comes with internal strength.
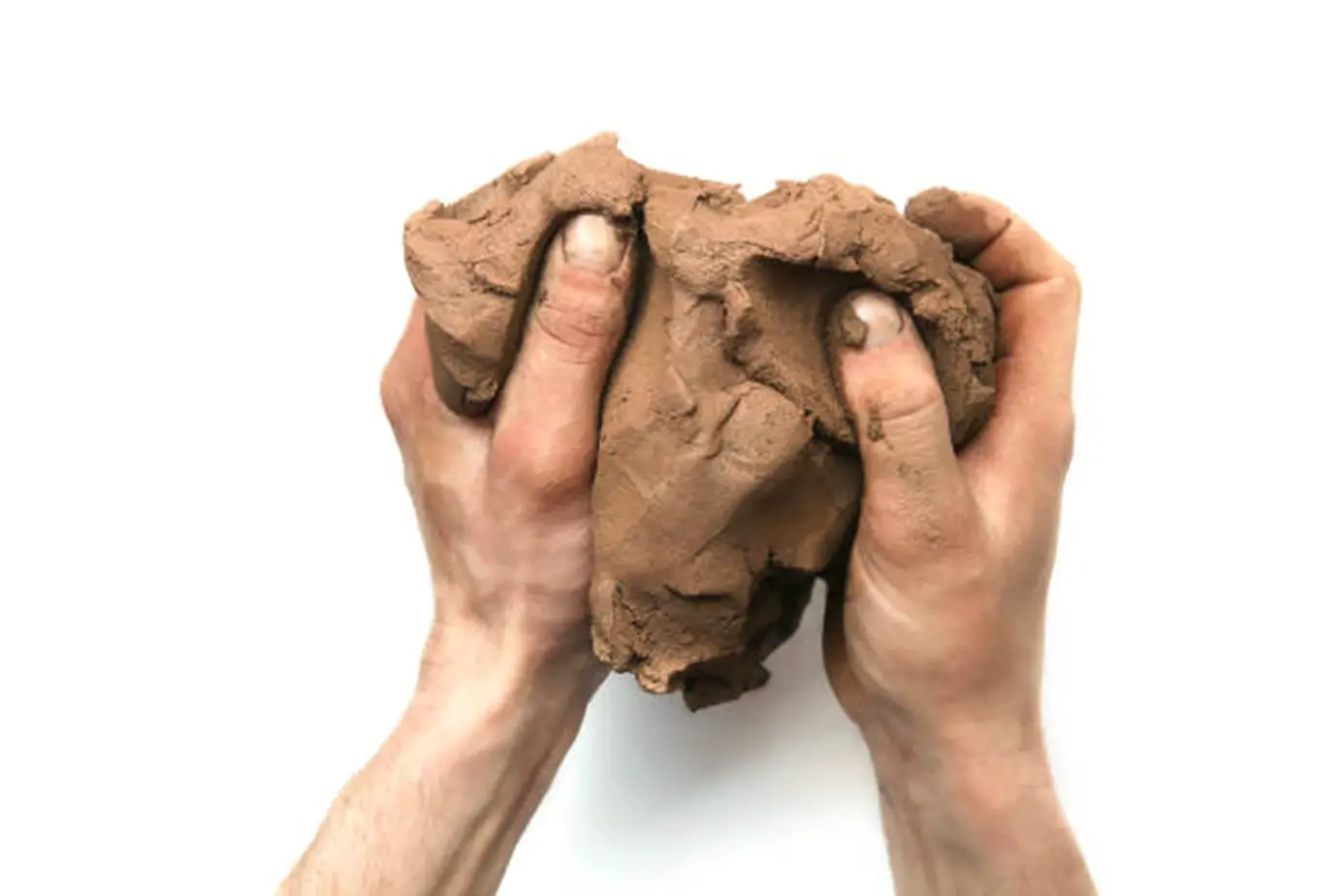
Here are the essential things to look at in the clay.
-
Ball clay content:
The ball clay content in the clay is going to add more strength to the pottery. It makes the surface stronger, which helps in adding more strength while you add the glazing.
-
Grog:
The grog is going to make your clay stronger. At the same time, it is going to reduce the amount of shrinkage in the clay.
Application of the glaze:
While applying the glaze, make sure you are not using tongs, as it can break the fragile greenware. You can use this technique with one-side glazing to acquire a successful application. In such cases, the airbrushing and spraying process is going to be best.
For obtaining the best glazing results, you can opt for Xiem Tools’ Short Cut Handcrafted Glaze Brush for Pottery & Ceramics, which comes with super-soft hair quality made from goat tail to offer maximum glaze absorption. At the same time, the wood handle with a German Birch design provides excellent grip and durability. With this brush, creating controlled strokes with a proper flow is much easier.
Conclusion:
So, what are you thinking about trying out the new raw glazing technique? Doesn’t it sound interesting? However, make sure you use a solid piece of clay to execute the process correctly and acquire success in your work.