Understanding the intricacies of warping and executing efficient preventive measures can considerably improve the quality of pottery. Carefully preparing the clay and using thoughtful forming techniques, strategic drying, precision while firing and high-quality tools like ribs can help prevent warping in pottery. In this article, we discuss all about warping in pottery. We start with understanding why warping might take place. Then, we move on to the 5 ways of preventing warping in your pottery. So, if you want to learn more, keep on reading!
What is Warping in Pottery?
Pottery is a well-loved craft all over the world. It requires skills, patience, and an eye for detail. However, sometimes, it might require more patience when dealing with the challenges that come with it. Within this complicated art form, artists frequently face a common difficulty called warping. Warping in pottery is frustrating when your meticulously made clay form bends or deforms throughout the drying and fire process.
Imagine spending hours crafting a delicate vase or an ornate bowl, only to see it twisted or malformed after fire. Unpredictable bending and twisting are caused by unequal tension or moisture distribution throughout the clay body. For example, you may have experienced warping while making a tall, slim vase. As the clay dries, moisture escapes faster from the external surface than from the interior, resulting in uneven shrinkage. This imbalance in shrinkage causes the vase to bend or tilt to one side, ruining your design.
Warping can also happen during firing if the kiln temperature rises too quickly or unevenly. For example, if you’re firing a considerable platter, the outside edges may heat up faster than the inside. This temperature gradient causes the platter’s outside edges to expand before the core catches up, resulting in warping or cracking along its circle. Understanding the reasons for warping is critical to preventing it in your pottery projects. Careful clay preparation, deliberate forming techniques, strategic drying practices, and precision in the firing process can all help to reduce the possibility of warping and preserve the integrity of your creations.
5 Tips to Prevent Warping in Pottery
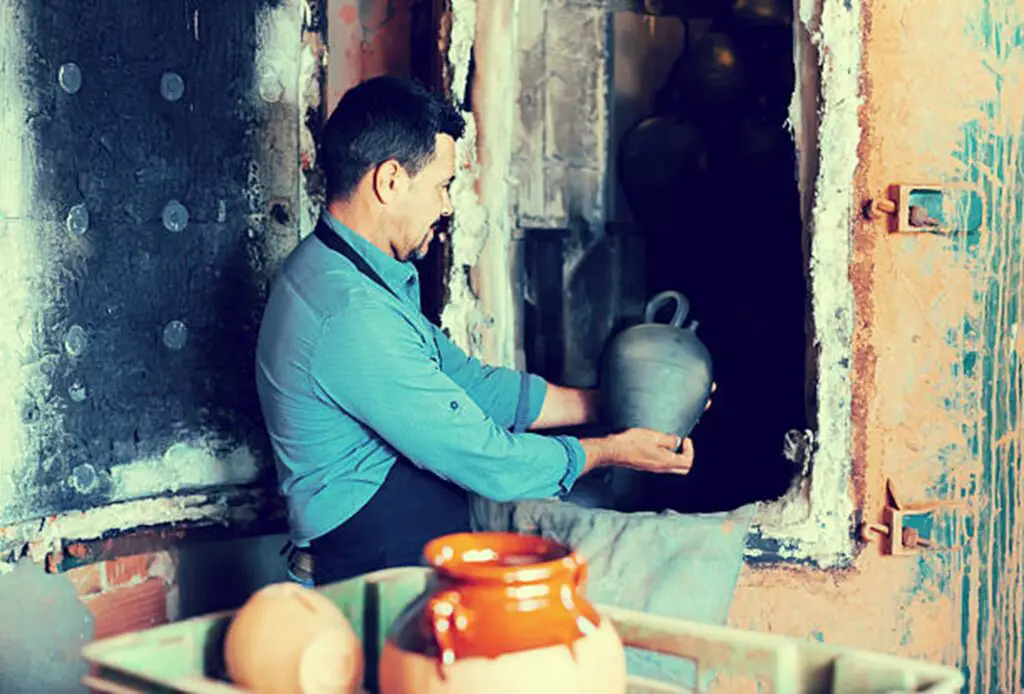
The artist must be meticulous throughout the process to avoid warping in your pottery. It applies to every stage of the process. Even from the beginning to the final firing in the kiln. Here are 5 things you need to take care of to prevent warping in your pottery.
1. Careful Clay Preparation
Begin your pottery journey by carefully preparing the clay as the foundation for fabulous creations. Knead your clay thoroughly to provide an even texture devoid of air pockets, which could cause uneven drying and warping later on. Choosing high-quality clay appropriate for your planned pottery type is essential; it gives the stability required to endure the stresses of forming and firing.
Say you’re working with a stoneware clay noted for its strength and resilience. By carefully kneading the clay and removing any air bubbles, you can get an even texture less likely to deform during drying and fire. This attention to detail in clay preparation lays the groundwork for a successful pottery project.
2. Thoughtful Forming Techniques
Use careful methods to ensure even thickness and uniform drying when shaping your clay pieces. Avoid severe thickness differences, as these can cause unequal stress distribution throughout the drying process. Whether tossing on the wheel or hand-building with coils or slabs, aim for consistent wall thickness to reduce the chance of warping.
Let’s say you’re hand-building a substantial serving platter. Using coil construction and ensuring an equal thickness throughout the sculpture decreases the possibility of warping as the clay dries and shrinks. Also, supporting larger or more delicate shapes with internal armatures or molds can help avoid distortion under their weight, ensuring that your creations retain their intended shape.
3. Strategic Drying Techniques
Proper drying is essential in preventing the possibility of warping. After making your pottery, use strategic drying processes to ensure even evaporation and reduce the likelihood of distortion. Avoid exposing your products to direct sunlight or heat sources, resulting in rapid moisture loss, uneven drying, and warping.
Imagine you’ve made a set of beautiful porcelain tea cups. Place them away from drafts and direct sunlight in a covered spot to promote equal drying and shape retention. Rotating the cups regularly during drying promotes uniform evaporation, lowering the possibility of warping or cracking as they lose moisture.
4. Precision in the Firing Process
When it comes to firing your pottery, precision is essential for reducing the possibility of warping. Follow proper firing schedules and temperature gradients to guarantee that your creations are heated and cooled in a controlled manner. Gradually increasing the kiln temperature provides for the steady release of moisture, avoiding unexpected expansions or contractions in the clay body, which can cause warping.
Follow a precisely calibrated fire schedule if you’re firing a collection of delicately glazed ceramic tiles. Also, when monitoring temperature gradients within the kiln, you can ensure that each tile receives uniform heating and cooling. This thorough approach reduces the likelihood of thermal stress-induced warping, ensuring the integrity of your completed tiles.
5. Use of High-Quality Tools and Equipment
Investing in high-quality pottery tools and equipment is essential to getting precisely what you want while reducing the risk of warping. Sophisticated tools for pottery, such as ribs, calipers, and throwing bats, provide greater control and accuracy, letting you confidently implement your idea. For example, ribs come in various forms and sizes and are used to modify the shape of your pottery during throwing or hand-building.
They help to compress the clay and guarantee uniform thickness, lowering the possibility of warping during drying and firing. There are a range of ribs available in the market. However, you can use the Byllstore Triangle Pottery Tools if you want the best tools available. They come with ribs and trimming tools that you can use to create pottery projects that don’t warp in the process.
Conclusion
You will find the abovementioned tips helpful if you want to prevent warping in pottery. You must be careful throughout the process of your pottery project. Careful clay preparation, mindful forming, strategic drying, precision firing, and high-quality tools such as ribs help prevent warping.