When it comes to dealing with high-temperature glazing, not everyone can master the art. At times, it could lead to colorant burn-off, or the material itself might become unstable when exposed to high temperatures. Whether you are a pro-pottery maker or someone who has just entered the profession, you could benefit from low-fire glaze recipes.
If you are someone seeking to bring uniqueness to your portfolio, these low-fire recipes are a must-try. Earthenware could be a tad bit harder when it comes to glazing, given the fact that its melting point falls a bit lower as compared to clay bodies.
However, you don’t have to worry about it, as you can do so much with the cone-04 glazing recipe that allows you to invest a range of unique colors into it.
So, without further ado, let us talk about the low-fire glazing recipes you can follow in your next pottery session.
Waxy-Matte Low Fire Glaze Recipe
This particular glazing process is amazing for your clay body’s firing and helps you achieve substantial results. It only works well for the cone numbers ranging between 012-09. So, in simple terms, earthenware is an ideal option for this glazing process.
Now, if you take a look at the recipe mentioned below, you might wonder why it doesn’t sum up to 100 percent. Well, the reason this has happened is the fact that it makes use of a part system that involves equal weightage as compared to percentage.
So, make sure you keep this in mind when making use of this glazing process.
To create this low-glaze mix, you need to have these ingredients:
-30 parts of Gerstley Borate
-10 parts of Silica Oxide
-20 parts of Kaolin
You must also consider that switching any ingredient in this mixture would require you to adjust the ratio as required.
Doing this to your pottery would create these particular looks:
- Matte Look:
If you are looking for a shine-free look to be added to your pottery item, this glaze mix will help you achieve the same with ease. Not every glazing process, especially in the hot glazing process, might not get a matte look. Rather your pottery would be the same old and generic shine-packed item that might or might not be something you like.
In case these proportions trouble you and a ready-made mix is what you need, you can take a look at this amazing product called the AMACO low-fire LM series matte glaze, which is lead-free and AP-certified for its non-toxic nature.
- The Waxy Look:
For someone who loves to create a waxy look, you will surely love this recipe. Although the colors might not look as vibrant and shiny as they would in normal glazing recipes, this surely brings class and elegance to your pottery.
This particular recipe is fairly simple to try and can be the best for beginner pottery makers. However, you also must know that this simplicity might not allow you to experiment. So, you might not be able to work around any changes to the recipe to create something different.
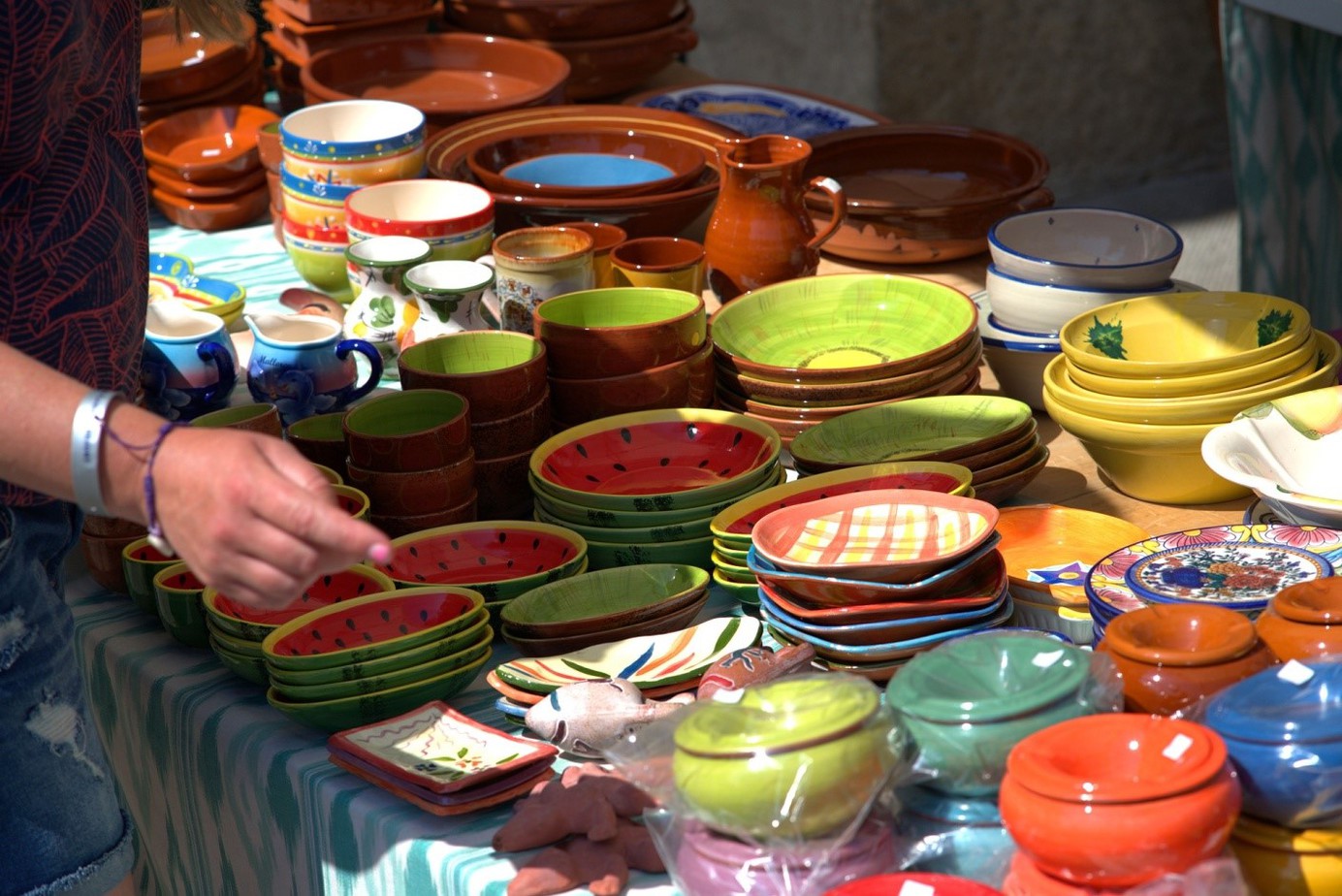
Red-Purple Earthenware Low-Fire Glaze Recipe
Are you bored of that traditional old & boring brown look that is achieved with your earthenware? If so, this is something you must surely try out the next time you are experimenting with your clay or earthen material. You must fire this recipe in the cone-04 glazing environment to achieve the right results.
Ingredients Required for Creating This Low-Fire Glaze:
-5 Parts of Whiting
-27 parts of soda feldspar
-39 parts of calcium borate-based frit
-23 parts of quartz
-.03 parts of cobalt carbonate
-5 parts of red stain or CdSe
-6 parts of China clay
However, in this process, you might have to be a tad careful during the firing process, and the same should be done in a particular order as stated below:
- Weigh all the ingredients as described above
- Now, pick the initial 5 ingredients & mix them all
- After you have mixed it up properly, then comes the next process
- Mix the remaining 2 ingredients & then mix them with the previous solution
- Doing this gets you a reddish tint that could be put on the earthenware
- This mix fires up ideally in the oxidizing environment that is Cone-04 to get the best results
The best thing about this glazing process is that you can add pretty purples to your pottery collection or any other color of your choice. However, stick to the process mentioned above, and you will get pitch-perfect results.
Curdle Blue Low-Fire Glaze
Another classic example of low-firing glaze is the Curdle Blue is perfect for someone who needs something unique and appreciated by your buyers.
However, there are several caution factors that you might have to remember by when trying this glazing process. Here are some listed below to help you fire your pottery safely:
- Don’t allow this glazing mix to fall or contact your skin
- Refrain from inhaling the fumes that might emerge from this product
- Don’t allow the product or fumes to enter your eyes
Among the ingredients used, Borax is something that could be very poisonous. This is why you need to make sure that you are working in an environment with proper ventilation. Apart from this, you must also wear protective gloves as well as lab goggles to protect the eyes.
Here is the ingredient list for this low-glaze mix:
-50 percent of Gerstley Borate
-50 percent of Borax
-0.5 percent of Cobalt Oxide (optional)
-3 percent of rutile
When you mix all these ingredients, it will provide you with a beautiful blue texture that looks particularly amazing on your pottery, something similar to Moroccan-style pottery.
Now that we have established the three easy-to-do low-fire glazing techniques let us check out the Pyrometric Cone Chart as per Orton Standard that allows low-fire glazing.
Cone Number | Temperature (Centigrade) | Temperature (Fahrenheit) |
08 | 955 | 1751 |
07 | 984 | 1803 |
06 | 999 | 1830 |
05 | 1046 | 1914 |
04 | 1060 | 1940 |
03 ½ | 1080 | 1976 |
03 | 1101 | 2014 |
02 | 1120 | 2048 |
01 | 1137 | 2079 |
1 | 1154 | 2109 |
2 | 1162 | 2124 |
3 | 1168 | 2134 |
Now, what you require from your low-firing glaze could vary from person to person. Whether you want a glossy base, matte base, or satin base would depend on the materials used. Here is an example of how you can achieve it via the classic cone-04 for low-glaze firing.
Base Type | Material/Compound | Percentage in Mixture |
Glossy Base | Ferro Frit 3124 Gerstley Borate EPK Kaolin | 30 40 30 |
Matte Base | Ferro Fit 3195 Whiting EPK Kaolin | 43 43 14 |
Satin Base | Ferro Frit 3195 Dolomite EPK Kaolin | 50 30 20 |
Does the glaze temperature matter?
We understand that different pottery materials can exist in varying states, such as solid, liquid, or gaseous. For example, your regular drinking water can exist as ice, steam, or liquid. The only difference in these states is the temperature.
Glazes are normally solid when kept cold or at room temperature. However, they start turning into liquid when heated properly with the use of a kiln. They even become gaseous when heated to a very high temperature.
You must understand the relation between glaze and clay. The commonly occurring red clay-like brick clay starts melting as it reaches 1100oC. This is why it is ideal for the creation of low-temperature items.
What are the advantages and disadvantages of Low-Fire Glazing?
Products such as whiteware, earthenware, terracotta, or low-temperature ceramics are fired within the low glazing temperature of 900 to 1100oC range. These products are termed earthenware. All these products have something in common, which is the clay bodies. This is what helps them develop the maximum amount of strength when fired within this temperature range.
They work best with glazes that have low-melting ingredients such as sodium, lead, or potassium.
Advantages of Low-Fire Glazing
- The best benefit that comes from low-fire glazing is the cost savings that happen in the process. Low-fire glazing can be done in a small electric-based hobby kiln. They can be plugged in straight into your electric connection supply, and your firing process starts.
- Plus, they are also easy to program or handle as opposed to the high-fire glazing processes.
- They require very little energy for firing and might not amp up your energy bills as they acquire maturity pretty easily. In short, your electricity bill would be way less.
- Low-fire glazing for earthenware brings out a wide range of bold and bright colors. The primary colors used for firing tend to keep the brightness as it is during the process.
- Low-temperature glazes are available with ease, and small pint-sizes compared to high-temperature glazes and are easy to paint.
Disadvantages of Low-Fire Glazing
- Low-fire clay or earthenware continues to be a bit porous and absorbs water. This can be made water-proof with the help of low-fire glazes. This glaze forms a beautiful glass-like layer all across its surface & hence seals the clay body’s porous texture.
Moreover, you would also need to seal the base completely with glaze, as an unglazed bottom would allow the water to get absorbed.
- If your low-fire pottery hasn’t been vitrified, any small or negligible imperfections in your glazing process could allow the water to seep in. It could be as small as a pinhole, and it would allow water seepage.
In case water enters the clay body, it would surely weaken with time and also harbor a lot of bacterial population.
- Non-vitrified clay that has been low-fired isn’t as strong as those fired under high temperatures. They also chip away very easily. This is why low-fire earthenware isn’t ideal for regular or functional needs. Daily knocks & bumps or washing might not be endured in the long run.
- Historically, most glazes used for earthenware were created using lead, which is pretty poisonous. Lead melted away with ease and made up for a great glaze component. However, today, you can find better and non-poisonous glaze materials that do not have lead.
Low-fire glazing is ideal for items such as vases that aren’t used much and kept as it is in a place that is safe from knocks or bumps. They can surely hold water but adding the right glaze helps create an amazing seal from water seepage.
Quick Tips for Glaze Mixing
When mixing the glazes, here are some tips that you must keep in mind before starting the firing process:
1. If you plan to add an extra compound to the mixture, ensure that other elements are balanced out in the same manner. In case you have a high amount of quartz or silica, it could change the effect other components have on your pottery item.
2. When mixing the components, make sure you use a glove and never work bare-handed.
3. Always mix the glaze mixture with about 10 parts of water or so depending on the required texture.
4. Before glaze firing, make sure you bisque fire the pottery item to help them provide better results.
5. When firing the earthenware, do not go higher than cone-02 as it could melt away due to the heat.
6. Not all low-glaze earthenware can be used as functional ware. So, when in doubt, it’s better not to use them for regular requirements.
7. A lot of these compounds present in the glaze could be toxic. However, they might not be just as toxic post-firing.
8. Watch out for faults or other crazings that might happen in case the pottery item is being used as functional ware.
Conclusion
Earthenware pottery tends to be easy & fun to craft given the fact that it contains natural elements and uses low-firing techniques. This technique helps you save a lot on the cost factor while bringing you wonderful items to be added to your pottery collection. So, do try this unique technique and experiment with your skills with minimal investment.