The Raku glazing method is an ancient Japanese ceramic technique that has captivated the imaginations of artists worldwide. This unique process produces stunning sculptures that are both effervescent and ageless. At home, Raku glazes with minerals, colorants, and flux can be created. This article will review some Raku glaze formulas and the instruments needed for the technique.
What is Raku Glaze?
Raku glaze is a mixture of fluxes, colorants, and minerals used to glaze ceramic objects suitable for raku pottery fire. The Raku glazing method distinguishes itself from other ceramic firing methods by exposing the pots to high temperatures in the kiln for an extended period. This unique firing procedure of heating the pots to high temperatures and immediately removing them from the kiln significantly affects them. This ceramic firing procedure produces metallic finishes, unusual crackling patterns, and brilliant, bold colors.
What Happens During the Raku Glazing Process?
Raku glazes are prepared by mixing different colorants and minerals. Once the glaze is ready and the pot is covered, it is placed inside the kiln. Inside the kiln, the chemical compounds in the glaze interact with the surface of the ceramic pot under immense heat. It creates stunning patterns and designs, and in some cases, even cracks are formed. When the pot is removed from the kiln once the piece reaches its desired temperature, the ceramic goes through a rapid cooling process, which creates the classic Raku effect.
Essential Equipment and Tools for Raku Glaze
Before we delve into Raku glaze recipes, learning about essential tools and equipment used during the raku pottery firing process can be beneficial. Here is a list of equipment we recommend for Raku glaze pottery firing at home-
- Protective Gear:
Heat-resistant protective gear is a must for every home glazer. The kilns of Raku pottery are heated at exceptionally high temperatures. Therefore, we recommend using Kevlar gloves, an apron, boots, and protective eyewear. It helps prevent burns in case of an accident.
- Metal Tongs:
Metal tongs are essential equipment for every potter. They help pick up the kiln’s lid, extract hot pots out of the kiln, feed the fire, and place and remove the pot itself. We highly recommend the Black Carbon Bent Foundry Crucible Tongs for handling Raku pots. These tongs are lightweight and have a crucible lip for a firm grip.
- Glaze Application Tools:
Numerous glazing techniques are used in Raku pottery firing. Some people dip their pots in the glaze, while others paint or spray them to achieve their desired effects. Some popular glaze application tools are spray guns and brushes.
4 Best Raku Glaze Recipes
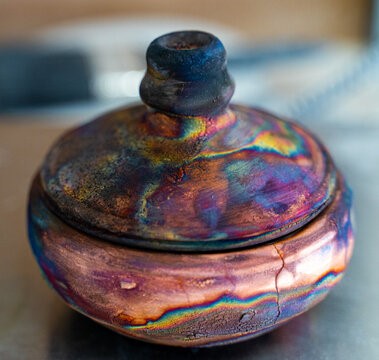
We have compiled a list of 4 famous and easy-to-achieve Raku glaze recipes for you to experiment with. These recipes are an excellent way to learn about various glazing processes, techniques, and functions of multiple ingredients.
Recipe 1 – Blue Moon Glaze
The first recipe creates one of the most stunning glazes for your ceramic kiln. It is a lovely blend of colors that evokes the splendor and beauty of a moonlit night. This glaze is easy to manufacture and has a stunning finish. Plus, this recipe allows for variations here and there as you wish.
Ingredients | Percentage |
Silica | 30% |
Frit 3134 | 20% |
Nepheline Syenite | 15% |
Lithium Carbonate | 15% |
EPK Kaolin | 10% |
Strontium Carbonate | 10% |
Tin Oxide | 7% |
Copper Carbonate | 4% |
Bentonite | 1% |
Preparation Steps:
- Carefully weigh each ingredient and pour it into the mixing container. Mix it with a stirring rod to ensure a uniform consistency.
- Once the glaze is ready, apply your preferred applicator evenly to the pot’s surface.
- Now, follow the standard Raku pottery firing procedure.
Recipe 2 – Traditional White Crackle Glaze
The traditional white crackle glaze recipe is popular because of its unique finish. This glaze produces gorgeous natural crackle patterns with a metallic luster during the pottery firing.
Ingredients | Percentage |
Nepheline Syenite | 60% |
EPK (Edgar Plastic Kaolin) | 20% |
Silica | 20% |
Preparation Steps:
- Combine nepheline syenite, EPK, and silica in a mixing container. Mix well to remove lumps. Leave aside for a couple of months.
- Add 1 to 3% copper carbonate to the glaze for a greenish hue and 1 to 3% iron oxide for a brownish tint. (Optional)
- Cover the pot in glaze and bake in the kiln for 5 to 6 minutes at 1000℃. Remove the pot from the kiln and let it cool naturally.
Recipe 3 – Forbes Cobalt Crust
The Forbes cobalt crust is another popular recipe. It is distinguished by its metallic yet earthy finish with reddish-brown hues. The glaze is simple to make and can be customized to fit your preferences. You can also add other chemicals, such as bentonite, for a brighter and more metallic appearance.
Ingredients | Percentage |
Gerstley Borate | 56% |
Synthetic Bone Ash | 19% |
Nepheline Syenite | 10% |
EPK (Edgar Plastic Kaolin) | 9% |
Silica | 5% |
Preparation Steps:
- Mix the ingredients in a mixing container. Add 8% copper carbonate and 2% cobalt carbonate to create a brighter, more vibrant glaze.
- Glaze the pot and bake in a kiln fired to 1100℃. When the pot is inside the kiln, use newspaper to reduce heavy post-firing.
Recipe 4 – Black Raku Glaze
This black Raku glaze recipe is perfect for creating a bold and dramatic pottery piece with a sense of mystery. Made with minimal ingredients, this glaze exudes a mysterious yet sophisticated attraction. As with most glazes, the ingredient amounts can be adjusted to get the appropriate depth of color.
Ingredients | Percentage |
Colemanite | 60% |
EP Kaolin | 30% |
Silica | 10% |
Red Iron Oxide | 5% |
Copper Carbonate | 5% |
Cobalt Carbonate | 2% |
Preparation Steps:
- Mix the ingredients thoroughly to avoid lumpy glaze consistency.
- Apply the glaze to the pot evenly.
- Bake in the kiln at 900℃ until the desired results are achieved. Let the pot cool down entirely, and the glazing process is finished.
Conclusion
The Raku glaze pottery firing process is a beautiful marriage of technical skills, tradition, and creative exploration. For pottery lovers, these classic glaze recipes can open a world of creative possibilities and teach them about the transformational nature of fire and glaze.